- 7
- 4
- 4
- 257 ha
Monthly Costs
Monthly Bond Repayment ZAR .
Calculated over years at % with no deposit. Change Assumptions
Affordability Calculator | Bond Costs Calculator | Bond Repayment Calculator | Apply for a Bond- Bond Calculator
- Affordability Calculator
- Bond Costs Calculator
- Bond Repayment Calculator
- Apply for a Bond
Bond Calculator
Affordability Calculator
Bond Costs Calculator
Bond Repayment Calculator
Contact Us
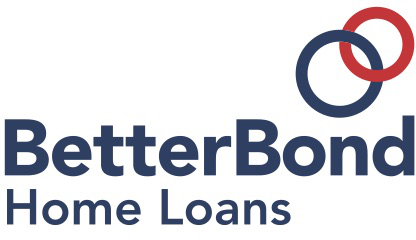
Disclaimer: The estimates contained on this webpage are provided for general information purposes and should be used as a guide only. While every effort is made to ensure the accuracy of the calculator, RE/MAX of Southern Africa cannot be held liable for any loss or damage arising directly or indirectly from the use of this calculator, including any incorrect information generated by this calculator, and/or arising pursuant to your reliance on such information.
Mun. Rates & Taxes: ZAR 1000.00
Property description
The land claim for the farm has been rejected by the Lands Claims Court. ( High Court).
This farm is a STUNNING find indeed: from the trees, to the de-husking facility, to the drying facility, to the cracking, roasting and oil bottling. State of the art , brand new equipment. The farmer focusses strongly on sustainability and ensures thar the best on-farm practices are used. .
The farm comprises of the following:
1. THE MACADAMIA ORCHARD: The Macadamia orchard comprises of 18 Blocks totaling approximately 150 hectare with 39 974 trees. They were planted with spacing of 9 x 4. The preparation has been done ( by the farmer personally), with a dozer, deep ripping all fields with 6 tons per hectare lime, and then rigged up. All the blocks of Macadamia trees have been planted on ridges, except 2 blocks due to topography. The farm considered as a flat farm. The varieties that had been planted are as follow: A4; A38; Beaumont; 814; 816; Nelmac2 and 863.
2. GRAZING CAMPS : Approximately 47 hectare had been divided into 4 cattle camps as well as 1 hectare and 2 hectare old cane fields areas. These had been fenced off for cattle and planted with Brazz grass, to improve grazing quality. Cattle paddocks and day camps are in place, crush all steel included concrete floor and steel gates, neck clamp, water drinkers in all camps and paddocks, all new fences made with CCA treated wooden poles and droppers.
3. CONSERVANCY AREA : The game/conservancy camp of 26.1 hectare had been fenced off with a 2 meter high Bonnox fence, all steel material. Inside the game camp is a 1.2meter high, fenced off camp of 2 hectare, where Brazz seed had been planted, The pasture is grazed controlled. The game consists of Blesbuck, Impala, Nyala, blue and grey Duiker, common Reedbuck. The total game count is plus minus 80 animals.
4. NARURAL BUSH AND TIMBER/ ROADS/ AND DAMS TOTALS ABOUT 38.5 HECTARES.
5. IMPLEMENT SHED : This shed of 600 m2 has a reinforced concrete floor, it is dozer proof with single phase AND 3 Phase electricity that had been installed with 5 foot, double neon lights. It is an all steel structure with white Chroma deck sheeting and cladding. The 2 lean-to’s, 1 on each side, are compacted G5 filling flooring with concrete strip in front, 180m2 each.
6. WORKSHOP : It is an all steel construction with Zink / sheets/ an attic / brick wall, roll up door in front and concrete floor. Inside is a separate tool room with above space made for storage. There are 3 phase and single phase plugs in the workshop as well as 5 Foot double tube neon lights, brick walls and steel windows ( as in the toolroom). The windows all have burglar bars and the doors are made of steel. One the left side of workshop is a lean-to with a concrete floor, all steel structure with a Zink / Aluminum roof, of 395m2 in size.
7. OFFICE BUILDING : It is a101m2 area and consists of a boardroom and 2 open plan office spaces as well as an archive, kitchenette, and fully equipped bathroom with warm water, a shower, basin and toilet. There are 2 built into concrete safes. It has all electrical roof/trussers, air-conditioner, etc. Newly renovated, the floors are tiled and there is a new electrical DB board, a phase failure DB board. All the windows and the front door are finished off with Trelidor for security purposes. There are an Internet Booster and a Nano Station Connection to provide internet for the house and school as well. A Security Monitor/ Hard drive Nano Station plus Omni Aerial had been installed and is connected to PTz Camera system at the entrance gate of the farm.
8. OUTSIDE BUILDING : This comprises of school area, a boat garage with a roll up door. There is a camping store room and a butchery room with a cold room built into the room of 96 m2. This is a brick building and is plastered with a concrete floor and Oregon pine refurbished doors. The school room is fitted with a 12000 BTU
air-conditioner and the windows has Trelidor burglar bars. It has a new green Chroma deck roof plus trussers. There are single and 3 phase electrical connection plugs and ceilings in the whole building with WIFI connection in building.
9. OUTBUILDING : It consists of a storeroom/ chemical room. It is an 133m2 area with, brick walls and it is plastered. It has a concrete floor with a Zink roof. Part of the chemical room has shelves and it has an aluminum/ glass front door, lockable ( for chemical control ). There is a store room part + solder. The rest of the building consists of a separate motor vehicle garage with a wooden door and with a ceiling.
10. THE BEE ROOM : This bee room has concrete flooring and brick walls. It has a chroma deck roof, a steel structure of 25m2 for the bees. It has an Aluminum window/door in the front. The building has 3 phase and single phase electricity as well as neon lights. We have 120 bee hives with supers and we have 4 different bee stand sites, where we pack our beehives. The idea is to do our own pollination and harvest our own honey. Therefor we have our own Bee Room to work in. Currently we have the help of our beekeeper to do our pollination.
11. DIESEL STORAGE : 5 x 2200litre diesel tanks adding up to 10 500 liters holding capacity. These are connected in line with electricity pump, counter and filling nozzle.
12.NEW DEHUSKING/ DRYING/ PROCESSING SHED FOR MACADAMIAS
DEHUSKING: 4 Lane pneumatically operated dehusker with 2.4metre tumbler with 20mm slots, all relevant sorting conveyors with light canopy, rerun conveyor and separate husk sorting conveyor with husk rerun to dehusker VSD controlled sorting table.
OUTSIDE: Hopper to tip nut in husk in sunken into ground, build out by bricks +- 6m3 holding capacity with conveyor VSD controlled to feed dehusker inside shed.
DRYING FACILITY: All done in galvanized material ; 150 ton holding capacity. All bins has got fans for each bin drawing hot air through a radiator heated up by a 300kw kettle. Bins totally enclosed on top with a moisture/RH probe with 2 extractor fan on each side of enclosed area to suck out moisture. Probe control electronically to be set to ideal RH level. The circulation of air in bins and fan corridor dry air out, thus drying nuts in bins. There is 21 bins of 7.5ton capacity per bin.
AFTER DRYING: The nuts get transferred via conveyor to a final sorting table, then split to either loaded on truck to be delivered to factory of choice OR to rope sizer for 4 different size grading, dropping in size holding bins, from there elevated into cracker out on shaker table, then to 2 x stainless steel tables for hand sorting OR to food grade sorting conveyor for grading. All nut processing equipment from cracker onwards made from stainless steel.
13. KETTLE: Our heat source made by a 300kw Bosman Boilers Kettle that supply hot water to the radiator inside the drying bin facility. Kettle in own building with IBR roof, steel structure on concrete floor, bought 2023 December.
14. MACADAMIA OIL PROCESSING BUILDING/AGRI PROCESSING : Built of bricks, asbestos roof and ceiling with concrete floor plus aluminum framed doors and windows, single phase and 3 phase electricity with various plug points, new DB board. Oelwerke 7.5kw Oil Press, cold virgin macadamia oil on a galvanized stand, oil drip into stainless steel bin. Transferred via mobile pump to another stainless steel bin on stand with own pump for filtering oil through a paper filtering system and from there gravity to next door building. Air-conditioner installed as well as glass doors and tinted windows.
15. MACADAMIA OIL BOTTLING/KERNEL PROCESSING BUILDING
Brick walls with PVC ceiling, plastered walls with aluminum windows and double door for entrance with concrete floors – single and 3 phase plug points. Two x 1000litre stainless steel holding tanks with ABC Hansen Gear pump, all connected via food grade hoses to pump in various directions to stainless steel bottle filler table, various stainless steel tables and brand new roasting oven and milling machine to produce macadamia meal. Also a moisture testing machine with printer to print out test results for every batch of macadamias pre-delivery to factory on PRE processing on farm, our processing involve making Cold Press Virgin Macadamia Oil with own press and filtering system, we have NO SOYA allergy problem, Roasting and saltery of kernel and macadamia meal for baking or flavoring. Airconditioning; tinted glass windows and doors.
16. STAFF ACCOMODATION:
Consisting of 16 rooms with ablution facility with showers, toilets and warm water, whole complex got own DB board, all rooms have prepaid electricity meters. There is a kitchen/cooking area as well.
17. WATER FILLING POINTS:
There are 17 Water Filling Points spread all over macadamia orchards and all on 63mm HDPE Class 8-to 12 poly pipe with steel upright filling points with layflex hoses on ends. Water for filling watercarts, spraying carts or fire carts. This water comes from 2 concrete reservoirs that gravity feeds into pipeline, one side has got a pressure pump to increase flow. These concrete reservoir = one on office inclosure roof of concrete and the other on top of silo with a ground tool shed at the bottom and top below the concrete reservoir. These 2 concrete reservoirs are supplied by 2 pumps, one on dam and the other one from a small fountain dam.
1.2km Cable in surfix or Armored cable and HDPE pipe. The 2 pumps regulated by float switches to keep the 2 reservoirs full. This concrete reservoirs supply garden and workshop as well as staff accommodation with water on a pressure pump system.
18. DRINKING WATER : This water comes from a borehole which is equipped with a pump that works on Solar, as well as electricity ( in case it has been overcast for a long time) and it switches automatically between the 2 sources. This pump fills 20 000litre (4 x 5000litre) water tanks that supply both houses with water via a pressure pump system with a float switch.
19. SOLAR BUILDING 7 X 5 METERS: This building has brick walls, plastered with an IBR roof and has ceilings. There are Aluminum double doors for the solar area with Aluminum framed windows, the second double door serves the generator room which has galvanized air vents for ventilation. The floors are concrete reinforced floors. Busy to finalize the Solar Project that is not installed yet but will be a 110kw installation.
20. GENERATOR: 150 KVA Perkins 6 Cylinder Turbo Air cooled with switchover (250 amp) installed and supply electricity in case of the need for electricity.
21. EARTHEN DAM has been enlarged and strengthened.
22. HORSE STABLES/ TACK-ROOM/ STOREROOM FOR FEED: There are 10 x stables open and ventilated, with brick walls on the sides and at the back, with concrete floors. There are IBR roofing and CCA treated poles, a lunging ring and 2 arenas. There are 5 grazing camps, all camps have water troughs installed and they are automated. The tack-room and veranda are used as a clubhouse. It has a bathroom and a steel cabinet to keep all horse tack and medicines safe. There is a newly constructed feeding room to keep all the feed needed nearby and safe from the weather. The 2 above mentioned buildings are made of bricks, has plastered walls, concrete floors and all windows and doors are secured with Trelidor burglar bars and security doors.
23. The NEWLY BUILD STOCK STORAGE SHED 18 X 30 meter steel structure; IBR Zink roof with gladding, a concrete apron all round. 2 LARGE doors open to this shed. A super-link truck can drive through, or park inside to offload stock or food. The floor has been filled and compacted G5. The purpose for this big shed is to be able to store bulk food for horses and cattle, fertilizer as well as macadamia shells for the boiler. It is also utilized to store shavings for the stables and surplus timber.
24. HOUSING: MAIN HOUSE: Has been renovated recently and has 5 bedrooms and 3 bathrooms; lounge; TV room; Entrance to house with bar and entertainment room with stackable doors and windows by big swimming pool, the back veranda with laundry room, big kitchen and tearoom. A big landscaped garden with fountain feature by the swimming pool. Bricks/ Plaster/ Tiles/ Carpets/ Zink roof/ 588 m2 with double garage doors with automated, wooden finished doors and there is extra garage 28 m2.
SECOND HOUSE: Totally rebuild in 2021/2022, new roof and cupboards, solid wood window frames and doors renovated; new bathroom/ kitchen cupboards, wiring and spacious at 139 m2. It has 2 bedrooms with 1 bathroom, TV room and a dining room as well as an office/third bedroom; veranda plus laundry/scullery space. Modern and beautiful.
EXTRA FLAT: To be renovated in the future 71 m2.
25. DOG KENNELS: This is a proper, enclosed, kennel area with a concrete floor in the residential area and there is a second, simiar kennel in the workshop area for the security guard’s patrol dog.
26. POULTRY PEN: 2 Proper chicken coops with open grazing on the one side, fenced off with diamond mesh and concrete at the bottom to keep chickens in and predators or dogs out.
27. NET HOUSE: For growing vegetables
28. FENCES: A HUGE effort went into fencing and is as follows:
(i) All fences are fully galvanized Bonnox mesh and only steel material, either treated or galvanized. Poles that has been concreted 1 meter deep in 0.5 x 0.5metre concrete holes. All the fences are as new and very well maintained and kept.
(ii) All the fences around the farm are 2 meters high with 8 electrified, single, steel wires and isolators on Bonnox
mesh with an alarm facility of 11 000 volts with 2 druid 18 Immobilizers on backup batteries to outlast power failures.
(iii) The conservancy fencing had been done the same as above, without electricity function.
(iv) The workshop and residential area have 2.4metre high Diamond Mesh with concrete at the bottom and also
razor wire on the outside from the bottom to the top.
The currently electrified fences keep all human, bushpig, buck as well as monkeys out that could be a big problem in damaging young macadamia nuts and destroy your crop.
29. GATES: The Farm entrance; Workshop entrance; Residential area as well as Dam area have proper galvanized sliding gates. The farm's entrance and camera works on solar system as well as a PT2 camera at the main gate. There is another 5 sliding gates all over the farm that operate manually.
GENERAL: Basically all buildings has got concrete aprons all round. The farm is very flat for the province and the area leans it to an easy crack out of 40% plus and higher on macadamias. The rainfall on average recorded over almost 20 years is 1350mm per year (report available) that gives us the opportunity to farm dry land without irrigation. We go to a lot of trouble to put down compos for the water retention and our soil preparations pay off to maintain the moisture level during drier periods, like in winter. The farm has been fully developed over the last 8 years by ourselves from a cane farm into a macadamia farm. An interested investor will grow with the farm as the trees mature and the harvest's yearly increase to its full capacity and turnover. Management/ Transfer Management negotiable; approved buyer/investor with funds available; sold as a running concern. All farm domestic animals excluded in sale. We do have a lot of surplus tools and equipment which is not in the sale, although parked or stored on same premises and the finer detail to be discussed, when the time is right. Give me a call....
Property Details
- 7 Bedrooms
- 4 Bathrooms
- 4 Garages
- 3 Ensuite
- 3 Lounges
- 3 Dining Area
Property Features
Video
Bedrooms | 7 |
Bathrooms | 4 |
Garages | 4 |
Erf Size | 257 ha |
Contact the Agent
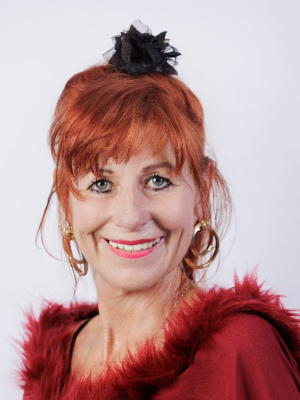
Linda Coughlan
Full Status Property Practitioner